Denny Hamlinwas sitting atop the speed charts after 30 laps of the early afternoon Cup practice at Martinsville Speedway. But his day quickly went sour when a piece of rubber jammed his throttle open, and in order to scrub speed from the car, he turned the steering wheel, sending his car crashing backwards into the wall. As soon as the TV announcers saw the significant damage to the right rear, they concluded that the No. 11 crew would need to pull out a backup car. Chris Gabehart, crew chief of the No. 11, and his crew at Joe Gibbs Racing, though, had a different idea. They brought in NASCAR’s Hawk-eye Optical Scanning Station (OSS) to evaluate the damage — helping them repair a presumed-totaled car in mere hours.
Here’s how they did it.
1:20pm, Saturday
Joe Gibbs Racing personnel and NASCAR officials begin examining the damaged No. 11 car. Gabehart was obviously disappointed to see such a fast car in disrepair, but didn’t hesitate in working with his group to start cutting off damaged panels. It took only 15 minutes to remove the trunk lid and rear bumper, and expose the damaged rear bumper supports. Initial observations revealed that the rear bumper supports had crumpled, which meant they had done their job to not only protect the driver, but also help prevent damage to the rear clip and fuel cell.
A NASCAR official observes the No. 11 crew and car while the OSS completes its scans.
Photo by: Bozi Tatarevic
1:50pm
Mechanics from 23XI Racing joined their Joe Gibbs Racing counterparts to disassemble the rear of the car as quickly as possible, and start preparing the car for the OSS. The OSS uses structured light scanning to measure bodywork and suspension down to a tolerance of 0.150 inches and while it is typically utilized for scrutineering purposes, NASCAR will also open it up to teams in special situations like this to see how far a car has shifted from its original measurements. Once a scan is complete, a heat map is generated comparing the bodywork to a CAD image of the car that’s stored in the system along with an alignment sheet showing measurements like camber and toe, much like you would see for a street car.
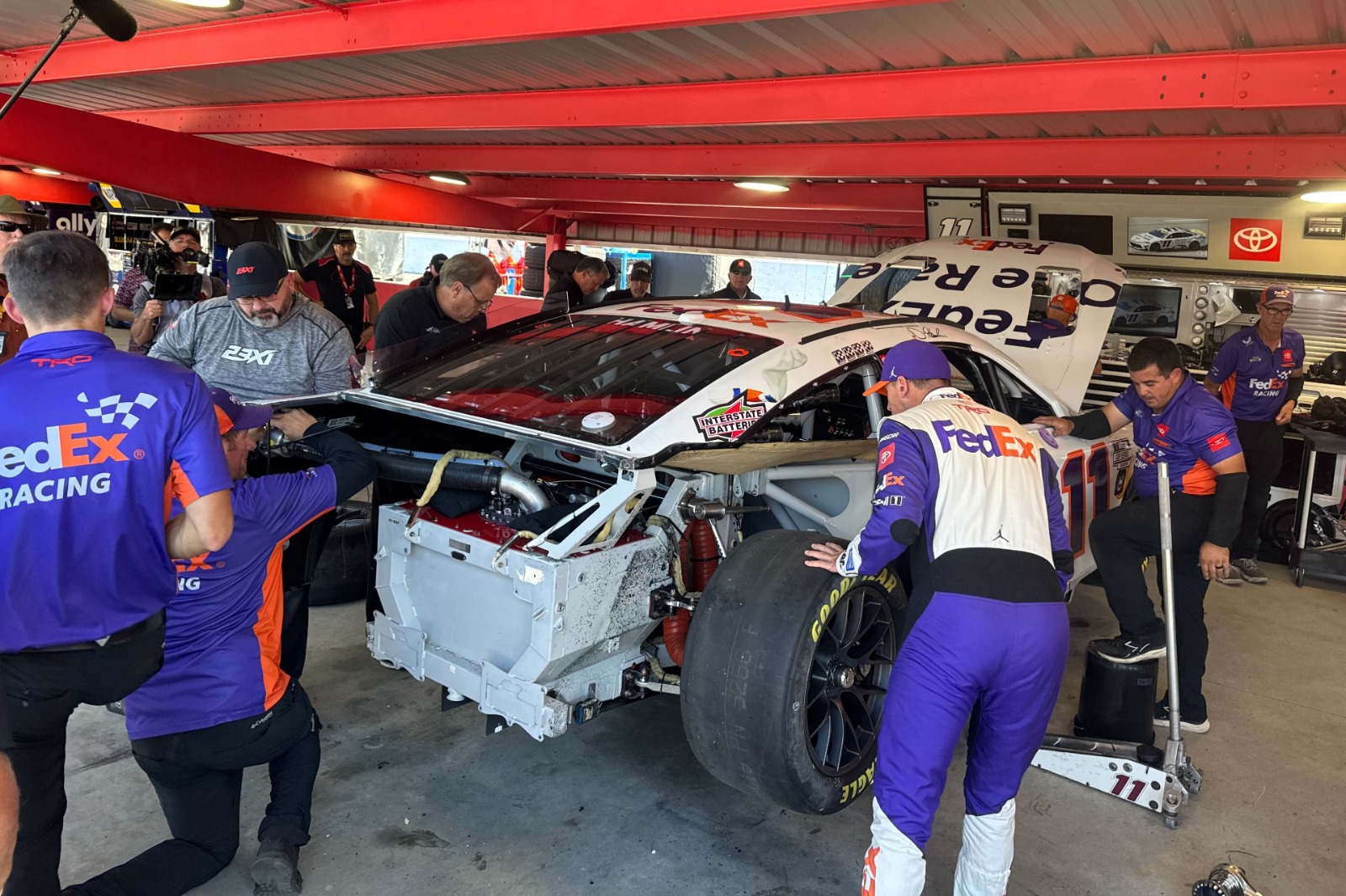
Denny Hamlin takes a look at the damage on the No. 11 while JGR and 23XI crew members continue to disassemble the car.
Photo by: Bozi Tatarevic
The opportunity to even consider these types of repairs is made possible by the modular nature of the NASCAR Next Gen car, which allows the chassis and bodywork to be assembled and disassembled in pieces. The previous generation car had a one-piece frame, so when incidents like this one happened, it typically meant going to a backup car as a repair would necessitate cutting and welding of the structural tubing.
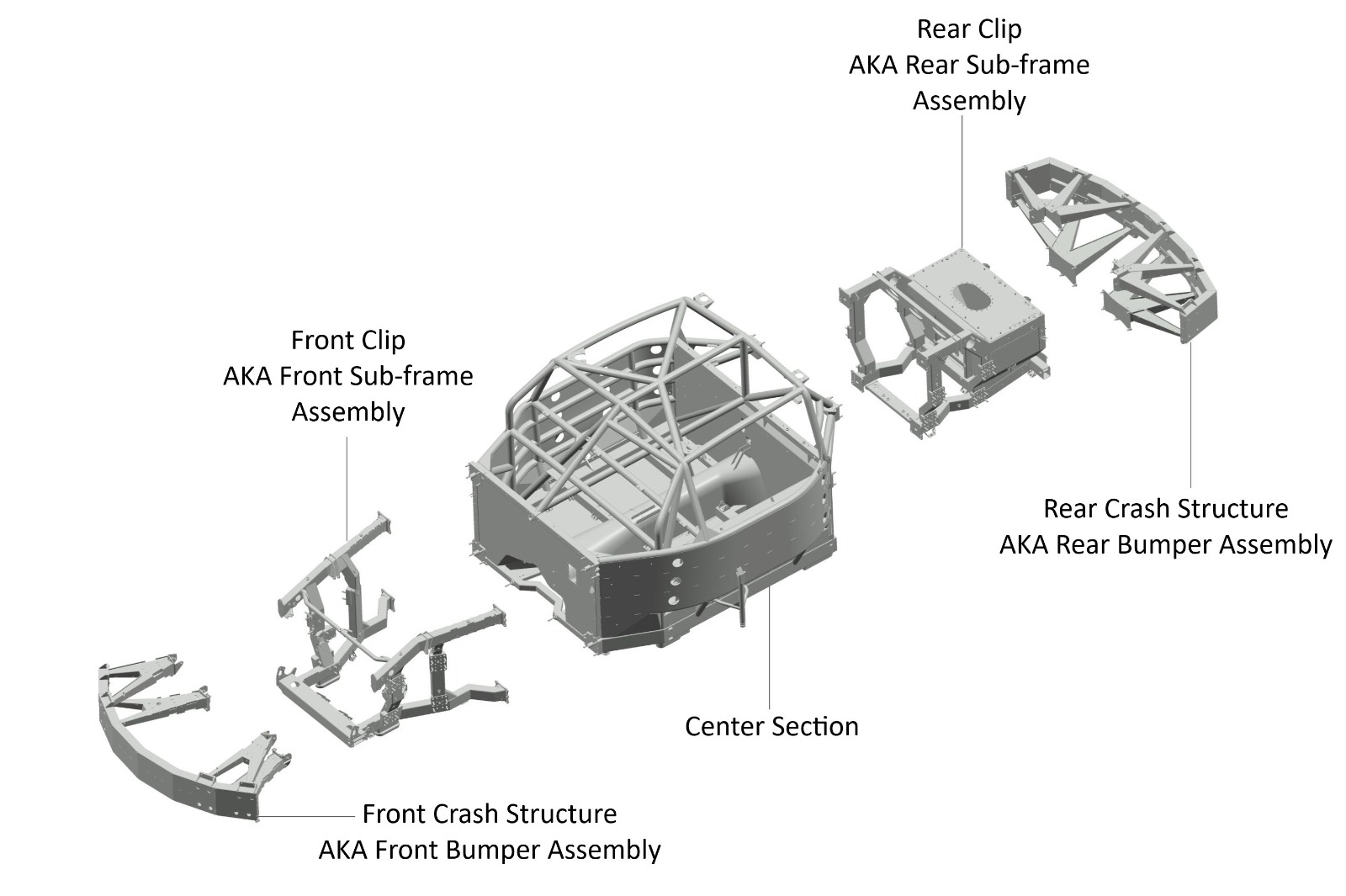
Photo by: NASCAR
Because the Next Gen chassis is built around a center section which is a safety cell for the driver that then has a front clip and rear clip bolted to it. Those clips then have bumper supports that are bolted to them that act as crumple zones for the car. The center section has four points underneath it that are used as reference points for the OSS scans. In the case of the No. 11, they were able to unbolt the damaged rear bumper support structure and unbolt the damaged bodywork, then quickly scan the rest of the components to compare them to their earlier measurements.
2:00pm
Crew members pushed the car over to the OSS. Fifteen minutes later, they were back in the garage with a decision to start repairs based on what the measurements showed. A large yellow box appeared on the liftgate of one of their trucks, which mechanics swarmed to grab needed components like a new bumper support along with bodywork.
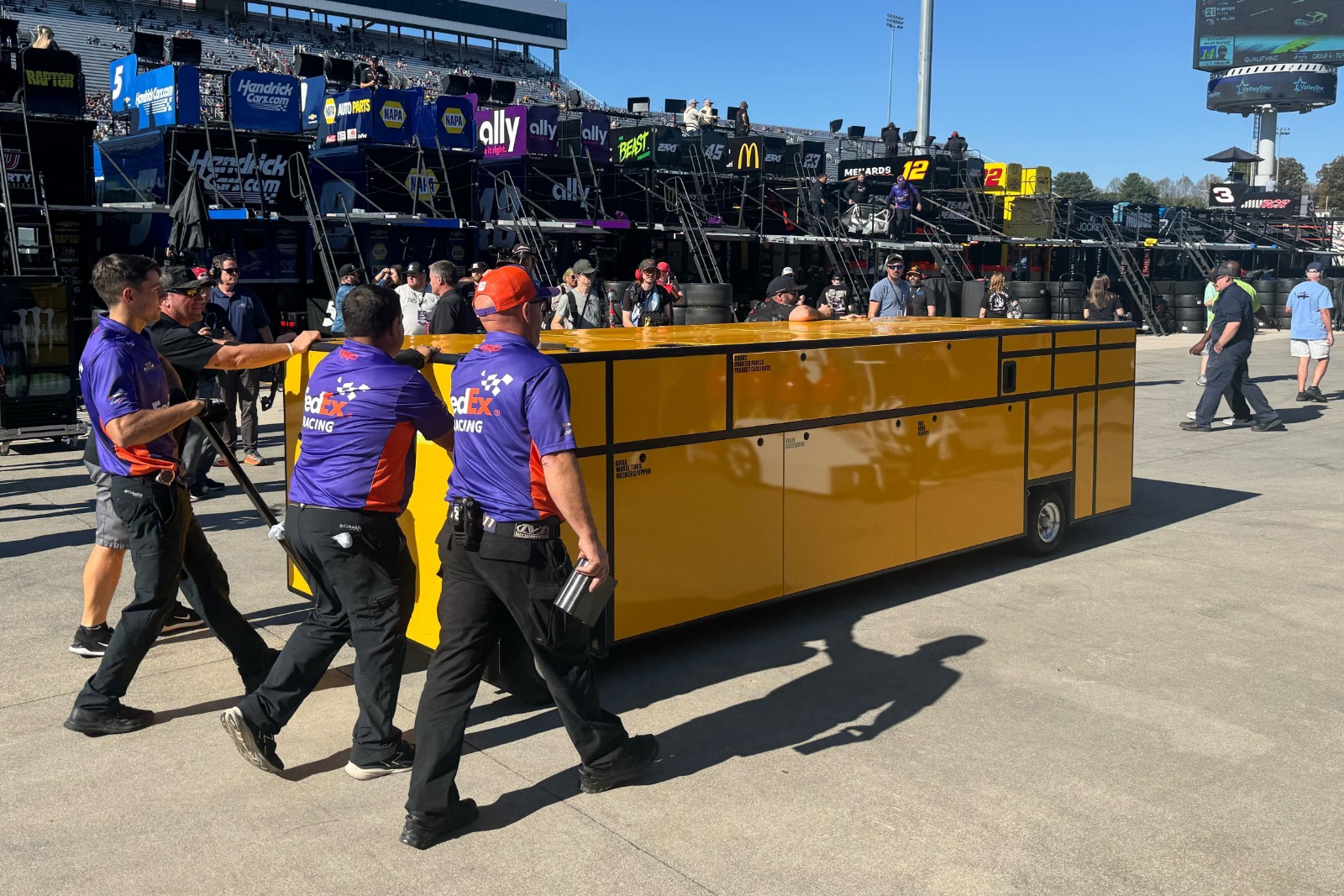
The crew of the No. 11 car walks a yellow compartment box on wheels to their garage.
Photo by: Bozi Tatarevic
Another helping factor to the speedy repair was the storage box that was organized in a way that made grabbing necessary components easy. The team employs a 5S organization method for labeling and sorting — which is not a surprise considering that Joe Gibbs Racing runs Toyotas and 5S is part of Toyota’s Kaizen philosophy.
Three Hours Later…
Parts were bolted to the car and the No. 11 team was setting wheels down to the ground for another run through the OSS to check their repairs. The now repaired car was in the same window as what it had shown during an earlier inspection. They brought it back to the garage for some tweaks to the right rear corner in order to get it to as near perfect as possible.
6:30pm
The car was back on the ground and pushed outside to test the engine, as well as verify that the throttle body would not have any additional issues. After testing, and happy with the measurements and appearance of the car, the No. 11 crew put it away for the night.
Race day, Sunday
Hamlin’s car goes back through the OSS and the crew decides to make a couple of final tweaks before pushing the car to the grid for the race.

Denny Hamlin, Joe Gibbs Racing, FedEx One Rate Toyota Camry
Photo by: Peter Casey – NKP – Motorsport Images
The modularity of the NASCAR Next Gen car allows for components to be transferred to a backup car fairly easily, but in the most ideal situations, using the car you’ve spent weeks working on is always preferential. In the case of the No. 11 car, the Next Gen car was easy to bring back to life after a significant crash and allowed the team to retain the car and speed that they saw in practice. And in reusing that fast primary car, they also avoided a long night of driving over two hours to their shop in Huntersville and spending ten to twelve hours working on a backup before making the two hour trip back.
Instead, they were able to complete a repair at the track in less than five hours. Allowing the crew members to wrap up before 7pm and be ready and rested for race day. Unfortunately for Hamlin, he would have to start the race in 37th place. But he would make his way into the top 15 before lap 100 and eventually finish the race in 5th place.